Construction is all about materials, and it is one of the resource-intensive industries. Among many other materials, cement is an essential binding material in any construction project. Considering the circumstances, the cement will remain the key material to satisfy global construction needs. Portland cement use started almost 200 years ago and since that its use has grown immensely due to its mechanical and chemical properties suitable for construction. Its durable, waterproof, and easily available. It is a vital component of concrete. According to an estimate, the world produces almost 10 Billion tons of concrete every year to satiate construction industry demand for different projects. Cement and concrete combined are the 2nd largest industrial emitters of CO2 globally. However, their demand is so high that the existing market business value of both these is 1 trillion USD. Studies by the different international agencies predicted that the demand for cement and concrete will keep on rising due to urbanization as by 2050 almost 70% to 80% of the world population will be living in cities.
The debate on climate change has led to the development of different solutions in almost every industry. Low carbon solutions can help to reduce the effects of climate change. We can also contribute to lower carbon emissions by revolutionizing the way we build our cities. Shifting to sustainable cement technologies that integrate the concepts of the circular economy are there to help us in reducing the carbon footprint of cement production. The environmental and technical benefits of shifting to sustainable cement production are enormous. However, the construction industry has been dormant in adopting those innovative solutions leading to higher carbon footprints of the industry.
The development of sustainable cement is an attractive option. However, there are many hurdles in the development process due to the plethora of issues. One of the major problems is the cost. The kilns are expensive to replace. The economic aspect of any alternative must be considered otherwise no matter how innovative and attractive the solution is, it is not going to work. According to the International Energy Agency, the main advantage points can be the use of alternative fuel, energy efficiency in the production process of cement, and alternative materials options. The cement manufacturers are introducing clean energy in their manufacturing process to reduce carbon footprint and achieved approximately 15% reduction in this endeavor. The efforts by the manufacturers have been recognized by the U.S. Environmental Protection Agency’s (EPA) Energy Star program.
According to the Solidia company’s claim, they have changed the recipe for the cement and gained exceptional results that can reduce the carbon footprint of manufacture up to 40%. They haven’t shared their chemical composition of the cement they have made but it uses less water to make and cure the concrete. Furthermore, it sucks CO2 from the air during the curing process which further reduces its carbon footprint. The chemical composition of the mixture allows it to cure at a much lower temperature than the usual Portland Cement.
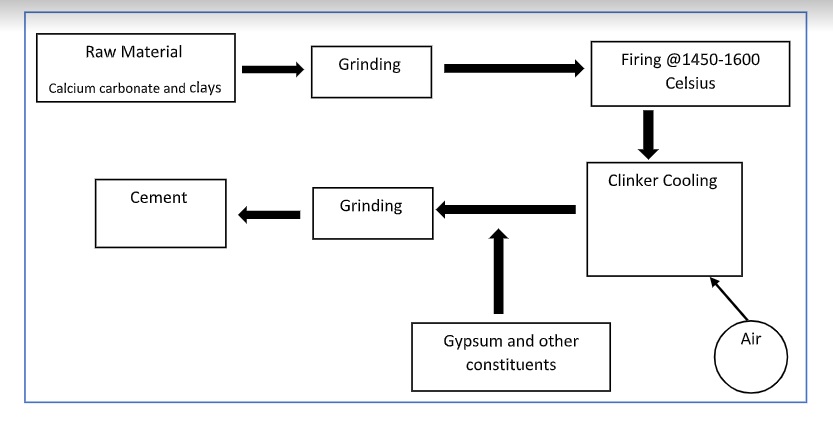
Sustainable cement can be manufactured by partially replacing clinker content with non-hazardous waste or alternative material options. A lot of research has been done in this regard and it has been proved that there might be problems regarding the availability of those alternate materials in different regions of the world but one thing is certain that the clinker content reduction is vital in this process. The clicker is the main component of most cement produced. Its presence results in the massive consumption of raw material containing calcium carbonate and clays coupled with high temperature. In parallel to the clicker process, a lot of grinding processes occur to obtain the final product having an average size of about 50 μm. According to the studies a little less than a ton of carbon dioxide is released for every ton of clicker produced. So, it can be inferred that sustainable Cement is the one that involves lesser clicker production. The European standard EN 197 classifies the cement available in the market based on their physical, mechanical, chemical composition, and properties.
The Cement manufacturing process is quite complex due to the secondary material options based on the use of the cement. However, the clicker is still the major component based on its mechanical strength development and quick setting time. The chemical composition of Cement can vary based on the materials used that can either be natural or artificial. Natural materials include calcium carbonate and artificial ones are fly ash, silica fumes, blast furnace slag, etc. The artificial secondary materials are important based on their role in the Cement hydration process. Usually, these materials come from the waste stream of different industries (semiconductor manufacturing plants, thermoelectric energy production plants, steel, and iron mills,) and can be counted as sustainable Cement. Projects aiming at Clinker reduction produced several alternatives also known as supplementary cementing materials. Ceramic residues, matt waste from glass, pulverized soda-lime glass, treated bottom ash, and activated slag have been tested as supplementary cementing material.
The new sustainable cementing materials have successfully reduced the clinker up to 30%. Reduction in clinker content sometimes improves the durability of cement when activated slag or pozzolan are added. These unconventional ingredients don’t seem valuable but when these materials are added with the right chemical composition, they provide sustainable Cement with enhanced properties. Sustainable cement production through alternative material options seems a bit attractive but it is vital to understand the other factors such as availability of that material, constant chemical composition, etc.
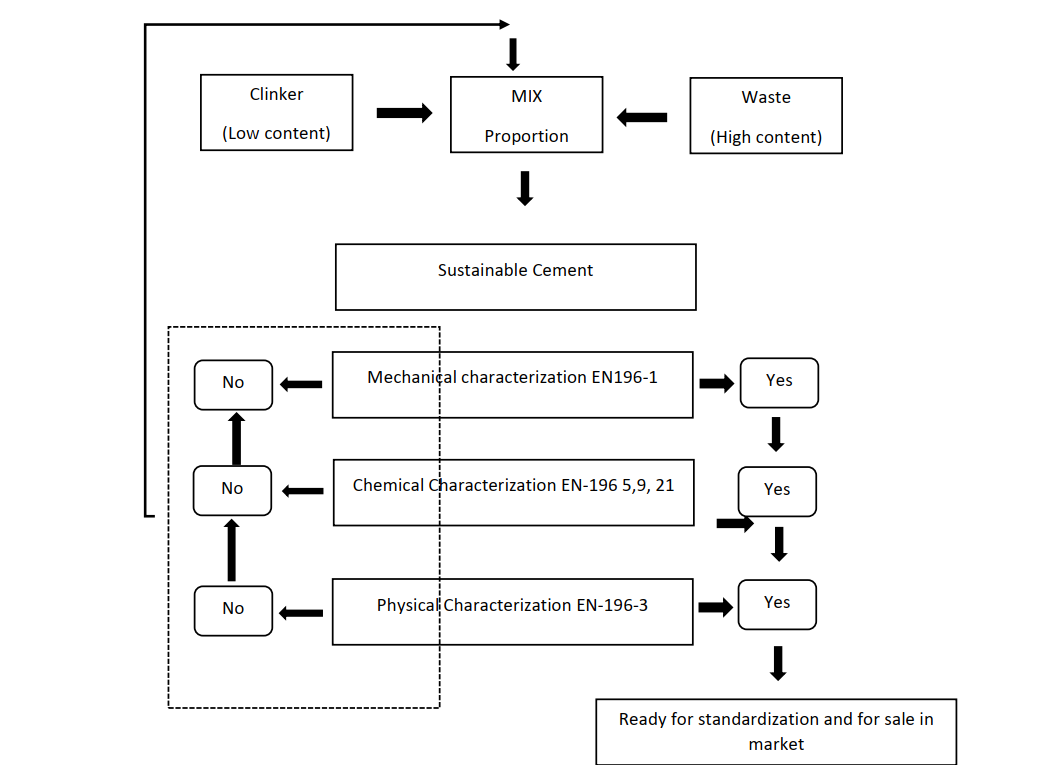
Globally many standards are being adopted to handle the types of cement, based on main constituents. Many countries have customized the standards and use national terms that classify the types of cement. European standard EN 197 is used for the classification of cement based on the clinker content. The following are the categories of cement based on the clinker content in their final composition.
- CEM I Portland cement (>95% clinker)
- CEM II Portland-composite cement (65-94% clinker)
- CEM III Blast furnace cement (5-64% clinker)
- CEM IV Pozzolanic cement (45-89% clinker)
- CEM V Composite cement (20-64% clinker)
To improve the process of clinker composition, there is a process known as mineralized clinker. In this process, the fluoride-containing materials are used to achieve a higher lime saturation level and therefore maximum contents of the alite phase. On the other hand, NaOH and Na2SO4 are used as activators or grinding the cement constituents finer to substitute the clinker.
Sources of secondary and alternative materials must be considered as the characteristics vary based on source and activation conditions. Geopolymer is a material used for a huge group of binders that solidify after the activation of a reactive solid in a highly alkaline environment. Geopolymers are produced based on Natural sources of aluminosilicates, for example, kaolin, and waste material like fly ash. There are several durability questions regarding the geopolymers. Whereas possible advantages include high early and/or final strength, good chemical attack resistance, and heat resistance. Instead of several benefits, the geopolymer’s use isn’t ubiquitous because of the high cost of activators, energy demand (linked to emissions), and availability.
Sustainable cement production relies on the well educated and trained staff at any stage across its supply chain. Similarly, the process of the production needs to be sustainable itself, in terms of raw material consumption, energy efficiency, and inclusion of material from other waste streams. Above all, the final product should meet the quality requirements coupled with the strength requirements. Research and development projects will continue to present different options, but the question will remain the same that either these materials are available for anyone and anywhere easily. The journey to achieve a truly sustainable cement is a distant dream due to the complex matrix of its properties, production process, availability of secondary materials, and much more.
To conclude, I would say, it is the need of the hour to decarbonize the economy by shifting to sustainable industrial practices. It will pave the way to maintain the balance between nature and the man-made built environment. To achieve that we should think of our construction materials and change the way we produce, consume, and reuse our materials. The most important material is cement. The complete transition to sustainable cement use can save CO₂ emissions from 1.72 to 2.75 billion tons annually. Furthermore, the extrapolation of these estimates to 2050 results shows CO₂ emissions savings from 7.25 to 11.60 billion tons annually. It is important to note that only producing sustainable cement is just one part of the recipe, design should be efficient as well to reduce the demand for the material.