Digital process solutions for civil engineering have been available for just under a decade and are now used throughout Europe. Digitization has become an indispensable part of road construction. What initially began with smaller special solutions quickly led to major challenges. These challenges and the developments that will change the construction industry in the near future are already foreseeable today.
In the last 10 years, infrastructure construction has changed more than in the previous 50 years. In the next five years, it will face the biggest changes in its history. Left unresolved are the problems of young talent and the challenges of an aging workforce, whether in the office or on the job site. In addition, an often false industry image distorts actual innovation in road construction, which is why innovation perceived from outside is far below actual. Wrongly so. Almost no other main trade in the construction industry, let alone in the stationary industry, has changed more in recent years and has seen higher productivity increases than road construction. The traditional fields of activity are becoming more demanding and complex In the process, the construction manager is increasingly evolving into a project manager. They are the interface to all parties involved and are confronted with new requirements regarding work preparation.
According to an interim trend, foremen are no longer just experienced machine operators with a coordinating function. They are already taking on management functions that were previously performed by site managers. In the future, the increasing demands on the client side will only be met by digital assistance systems. It is precisely this change that must be understood as an opportunity and actively shaped. Although digitization cannot solve these problems immediately, it is a path to a successful future.
This development did not come suddenly. What began about eight years ago with BPO ASPHALT has since developed into a comprehensive digitization solution for the entire road construction industry. BPO has long since been used to plan more than just asphalt construction sites and reduce downtimes. As early as 2016, the overall BPO system included modules for asphalt, concrete, milled material, earthworks and building construction. A short time later, at the customer’s request, the processes for job planning and for recording laboratory data as well as the digital delivery bill were also mapped. Initially, these processes could only be optimized in isolation. A step in the right direction, but only the beginning of something big. The strong increase in the number of users worldwide and the desire to holistically optimize all processes in the company created new challenges that could only be solved by a radical measure: The complete redevelopment of BPO.
The starting signal for the new development was given at the end of 2017. The new system was to bundle all process solutions for civil engineering in a powerful interface and make the input system even simpler and more intuitive. To ensure that this was successful, the office and administrative processes at several pilot customers were examined in detail over a period of several years. The result was a comprehensive process model. All roles, such as secretary, estimator, site manager, operations planner, mechanical engineer, foreman, and even paving foreman and accountant, were integrated into the new system. This ensures that all employees in the company are networked. This creates a digital work flow platform and the first ever technical ERP system for operational construction processes in infrastructure construction. The new system is called BPO INFRA and will integrate or partially replace existing BPO solutions.
BPO INFRA Module overview
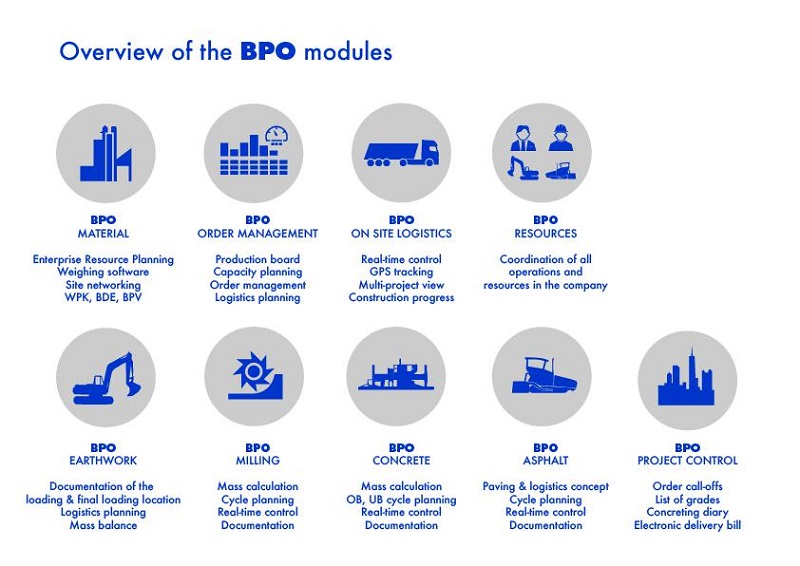
Digital work preparation in infrastructure construction
BPO INFRA covers the complete work preparation of all civil engineering projects from the smallest construction site to large projects. The construction manager can enter the project’s schedule with just a few clicks and create the construction schedule with all trades. In addition to the main processes such as asphalt or earthworks, secondary processes such as traffic safety or road marking can also be planned. Standard processes and individual processes can be defined for each organizational unit. If required, the site manager can also define process templates himself. This enables standardized construction time planning and a cumulative evaluation of the planned operating days for the various processes. Requirements for personnel and machines can also be planned and assigned to the respective trades and operating days. This information is then available for the scheduling of man, machine and material.
As soon as a project day is created, the material order can be sent digitally at the push of a button. All delivery locations, the truck logistics and the construction site can be networked in real time from the start of the delivery without any additional steps.
If a main trade, such as asphalt paving, is to be further detailed, the construction manager can plan the respective process precisely by means of construction progress planning. For this purpose, the digital road geometry can be imported directly from a CAD system via a BIM interface. If no other CAD system is available, a drawing can also be imported into BPO and the quantity takeoff is performed directly in BPO’s own CAD module. As soon as the masses have been calculated by the system, construction stages are formed and assigned to the respective work days. If schedule deviations occur, they are automatically synchronized with the construction schedule. Manual transfer is completely eliminated and all planning documents are always up to date.
If logistics pose a particular challenge, construction time planning and construction sequence planning can be supplemented with takt planning. Based on the planned construction progress speed, a cycle is calculated, which specifies on a minute basis the time interval at which the deliveries should arrive at the construction site. All deliveries are calculated to the minute and digital schedules with delivery time specifications are determined for each driver. The planned end of paving is determined and checked for plausibility with the information from the construction schedule and the construction progress schedule. The minute-accurate default values are available during construction at the delivery points such as mixing plants, the haulage company, the truck drivers and on the construction site in order to control the construction progress in real time.
Digital workflow and control of business processes
The data collected during work preparation, are available in real time in all important organizational units. In this way, all project data can be bundled at the senior construction management of an area to obtain an overview of the workload and to design the entire project planning without time conflicts. The data is also displayed at the operations planner or technical dispatcher, who uses digital demand reports to select the appropriate employees and equipment from his pool of personnel and machines. The dispatcher is optimally supported in equipment assignment by displaying the expected last location for each machine and sorting the machines by distance to the new destination. This ensures that the dispatcher is always automatically shown the closest resource first and that unnecessarily long machine transports are avoided. Thanks to the integrated collision management, scheduling conflicts and double-occupied machines are recognized immediately and can be resolved with just one mouse click. All resource categories as well as the personnel and machine master can be flexibly stored in BPO INFRA or automatically transferred from upstream systems through interfaces. The scheduling time frame can be flexibly selected. In addition, there is a day-specific scheduling view, which is structured as an interactive checklist to ensure that no job site is forgotten in the short-term planning. The machine diary is integrated and each resource can be evaluated according to its degree of utilization. All deployment and equipment data is passed on to the foremen and supervisors via the BPO INFRA app.
They receive information on the location of the construction site, including a navigation solution, as well as the activities to be carried out on the respective day. The foremen can request additional machines and equipment via the app, but also record the equipment used via GPS. The equipment is thus assigned to the correct cost center. At the end of the day, the performance report or daily construction report can be filled out. For this purpose, the integrated photo function can also be accessed. The current performance data, but also machine failures, can be recorded precisely to the addressee. PDF reports can be generated from the information, handed over to the client or the data can be transferred to other systems via interfaces. This includes, for example, the recorded working time, the hourly billing and the performance report for prompt post-calculation. This results in a target/actual comparison of the calculation and the budget is always kept in view.
Digital construction progress in real time
If the construction progress is to be monitored in real time during the paving day as part of a target/actual comparison, BPO INFRA offers many new possibilities to digitally support the main trades such as concrete, asphalt, earthworks or milling. In the asphalt plant, the mixing plant, truck logistics and construction site are networked in real time. In Europe, there are already interfaces to more than 700 mixing plants from which the delivery note data is sent automatically to BPO INFRA. The data is processed there and made available to the foreman on the construction site. This creates the virtual supply chain. At the construction site, the foreman is shown all information about the construction site via his tablet. He receives the current status of the tonnage already unloaded and still to be delivered.
Trucks can be integrated in various ways. For this purpose, the mobile tracking solution BPO Live is available, which is available for iOS and Android smartphones. Professional GPS reception quality is also available via special BPO trackers. Through almost 100 interfaces, however, more than 6,000 trucks can also be tracked via GPS using the fleet management systems available on the part of the forwarding companies without additional hardware or software.
As soon as a delivery bill is printed, the delivery note data is sent to BPO via an interface. The data is processed into a PDF delivery bill, which can be digitally signed by the foreman on the tablet PC or smartphone during unloading.
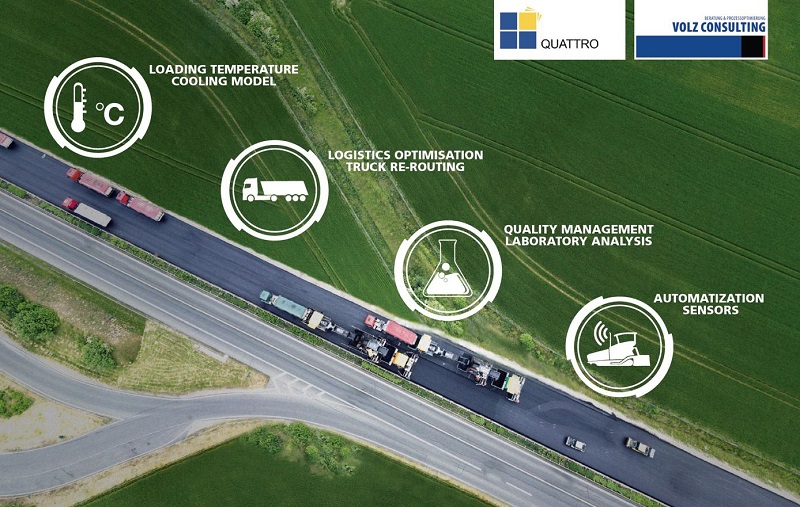
For example, thermographic camera systems can already be integrated into BPO in real time since 2015. The thermography data can be assigned to the delivery bills in the construction data model. Systems for area-wide dynamic compaction control (FDVK) and for the documentation of rolling passes can also be integrated into BPO across manufacturers. Since Volz Consulting GmbH is the only manufacturer-independent platform, a wide variety of construction equipment manufacturers and sensor suppliers can also be integrated.
Samples can be recorded with pinpoint accuracy using the laboratory module and the degrees of compaction can be determined. The laboratory technician’s test report is automatically generated from the data and sent. Via an interface to the layer thickness gauge from MIT, these values can also be automatically integrated into the BIM data model.
With BPO INFRA, a comprehensive BIM to field system, Building Information Modeling, is created, which enables the IT data to be made available on the construction site, collects the real-time data from the construction site and makes it available for processing.
Analysis
In the analysis module, all individual data in the building data model are causally linked with each other. This creates an effective quality management tool. In the case of defects, it can easily identify the parameter setting or the process participant to which possible defects can be traced.
At short notice, the target parameters can be compared with the actual parameters every day and the planning optimized accordingly. As a result, downtimes of the trucks can be avoided and paving is accelerated. In everyday operation, increases in paving performance of between 30% and 70% are possible.
BPO INFRA will become the most important milestone in the digitization of road construction. For the first time, the complete work preparation of the construction manager has been digitally mapped in a planning system and brought to the construction site in a BIM-to-field approach. BPO INFRA’s predecessor systems have already been in use for more than 7 years, so the foundation for a sustainable transformation is in place.
Volz Consulting GmbH is the only owner-managed software company for process optimization in the construction industry. It is self-financed and completely independent of manufacturers and investors. The business strategy relies on long-term and reliable partnerships to enable customers to adapt digital solutions to their individual requirements. A decisive added value of the customers lies in the manufacturer-independent system structure, as well as the platform and development neutrality.
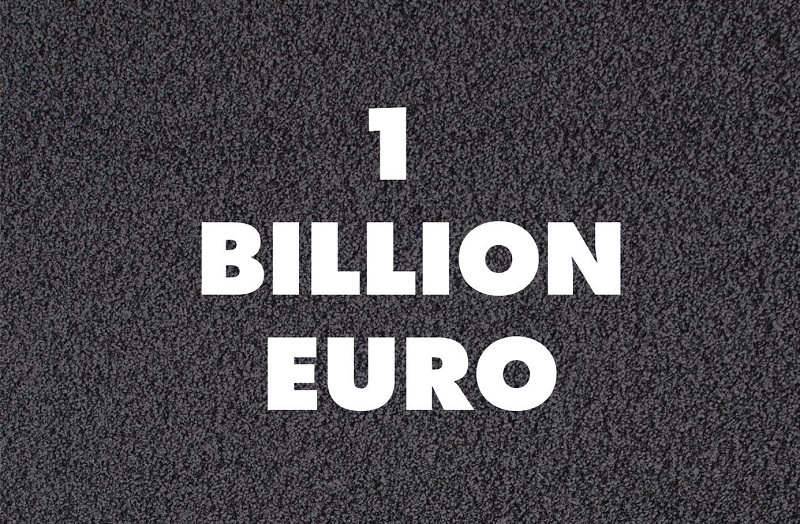
With more than 80 customers, BPO is the most widely used system for digital process optimization in road construction worldwide. With customers such as GÜNTER PAPENBURG, EUROVIA, STRABAG, WOLFF & MÜLLER, JOHANN BUNTE, VOGEL-BAU, MAX BÖGL, FAHRNER BAU, STOLZ and many more, BPO has become an integral part of civil engineering and road construction. In more than 10 languages, all BPO customers pave about 70 million tons of asphalt per year. In 2019 and 2020, masses with a financial equivalent of more than one billion euros were moved via BPO. This makes BPO the world’s largest digital platform for optimizing operational construction processes.
Source: VOLZ CONSULTING GmbH Press