The Middle East Prefabrication and Modular Construction Summit 2016
16- 17 Feb 2016 | Hotel Conrad, Dubai
Amr Metwally was interviewed by the team at Information Exchange Group ahead of their upcoming event The Middle East Prefabrication and Modular Construction Summit 2016.
Tell us something about Hamad Medical Corporation’s projects. What are the interest levels of the developers in incorporating the upgraded methodologies of the construction?
Qatar is facing big demand for the different healthcare services, excepted to reach 14.4% growth rate in terms of rising costs and demand for services from 2013 to 2018, which is a big percentage even though with expected slowdown due to the oil prices that won’t reduce a lot from the expected numbers.
In addition the rollout of a national insurance plan in Qatar since last year, increase in the demand for services is expected, as more people will be able to afford treatment.
In light of the big demand of increasing and expediting the construction of the new healthcare facilities, the need came for looking to upgrade the current traditional methodologies of construction to modern ways like modular building not as optional view but as potential mandatory change that can face the increase in demand. This responsibility of looking to new methodologies is not only coming under the client side but also under contractors as well as consultants.
In our case, we look to the new methodologies like modular buildings not only for potentially cost and construction period reduction but also for quality reasons. Building off site ensures better construction quality management as in case of modular construction. Materials that are delivered to the plant location are safely and securely stored in the manufacturer’s warehouse to prevent damage or deterioration from moisture and the elements. Manufacturing plants have stringent QA/QC programs with independent inspection and testing protocols that promote superior quality of construction every step of the way.
Beyond quality management and improved completion time, modular construction offers numerous other benefits to us. Removing approximately 80% of the building construction activity from the site location significantly reduces site disruption, vehicular traffic and improves overall safety and security. We are especially building most of our facilities in our very busy running Medical City campus.
With infrastructure projects being designed and constructed at massive scale, how prefabrication and modular construction as a module are helping in the architectural area planning, drafting, and building level?
For architects and owners alike, modular construction companies today can work with levels of design and construction sophistication that exceeds all expectations. It is beneficial that when exploring the various project delivery methods, when offsite construction is chosen early in the design development process, this allows all parties involved in the construction process to know their responsibilities and help to avoid the stigma of “Redesigning” as the project will be built around that methodology.
Also if off-site construction is considered during the design stage this might potentially allow for early starting of the super structure while the design being in development stage subject to the good planning and clear responsibility matrix between all parties with clear target and output.
In my view Modular construction must come with well-developed Building Information Modelling (BIM) as this will minimize the risk of design errors during the manufacturing process and will allow for a design to be properly tested for clashes and clearance zones, as well as the construction sequence before manufacturing which leads for better planning during the project phases.
What are the benefits and/or challenges faced in incorporating prefabrication and modular construction module vis-à-vis traditional construction methods?
There are many pros and cons between the use of Modular construction and Traditional construction. Shortened site construction time considerably is a clear benefit for modular case. Also, reduced health and safety risks during construction, minimized waste and maximized value as lean management concept, potential reduction in the building foot print, benefitting the current skills shortage especially with over 95% of labors used in construction are from outside GCC countries, better QA/QC as most construction is being built off-site and most importantly the impact on the community during construction can be significantly reduced in terms of noise, traffic and period of work on site as well as great impact on the environment especially with the potential energy saving for these kind of buildings.
With that still there are many challenges with Modular building like the narrow abilities of design changes compared with traditional method that can allow more for later design changes during construction. On some sites, it becomes very difficult to use modular due to the difficulties of allowing access for large modules and no provision of adequate lifting equipment. Biggest challenge for me is the limited opportunity for a localism approach to construction which can be decreased in case of Modular construction as it reduces most of the need for local suppliers and sub-contractors in light of the shortage of local capabilities of modular construction contractors compared with traditional ones.
How do you ensure sustainability of the infrastructure project without affecting the cost estimation and how prefabrication / modular construction come to your rescue?
In my view as stated earlier Modular construction must come with well-developed Building Information Modelling (BIM) as the potential way for minimizing the risk of design errors during the manufacturing because of the parametric nature of the model, and how it relates to the project as a whole. Because the project labor is moved off site, various project scenarios can be explored within BIM, saving both time and money. Potential problems can be identified early in the design process, saving time. Greater control of the final product is realized with the use of BIM.
I can’t see good development of modular construction without benefiting from the major increase in BIM technology as well as the benefits from the rising of new technologies like 3d Point Cloud scanning, 3d printing technology, CNC material processing etc.
It becomes a win-win situation due to right integration and synergies between modular construction and those technologies eliminating most of the risks during construction or at least reduce it.
How can the designing and architectural stages incorporate changes through prefabricated material in medical settlement?
As said before challenges with prefabrication or modular construction methodologies include constrained changes during the different phases with increased relation in moving from upstream to downstream. In other words, Changes are easier on the beginning and more and more difficult as moving forward in the project. This of course is related to external and building super structure.
However, for internal fit out modular concept even though it’s the same concept however it allows flexibility for future changes or future expansion as it can be amended easier compared with traditional construction.
Simulation instruments should be used during design changes as it gives a full idea of how the building will behave, the energy consumption, HVAC strategies, patient, visitors and clinical work flow etc. and for a clear vision on the output and position the required changes at the right phase.
What are your views upon the summit agenda and what are your expectations from the summit?
In view of the current situation and the expected slowdown in construction due to the reduction in Oil & Gas prices, I think it’s the time now to think smartly of how our performance was in the last few years, what was our evaluation of our construction practices and how can we be improved for the future.
This event should give the right facts for the benefits of adopting new methodologies in construction to all parties involved in the process whether clients, consultants, suppliers or contractors.
Questions like how we can support that from the client point of view and what we expect from consultants and contractors communities should be answered in transparent ways by creating platform for exchanging ideas, experiences and successful case studies.
Construction this year certainly will be different and more difficult from last year and on the other hand demand and expectation still as it is from the community for healthcare services provided if not increased, so how we can maintain that with all current challenges is big question to be answered during this event.
I am really excited about this specialized conference on such an important topic after many years as it was discussed only as a slide presentation from individuals. But now I am looking forward for meeting many experts to listen to their knowledge and successful stories in such rapidly growing field.
.
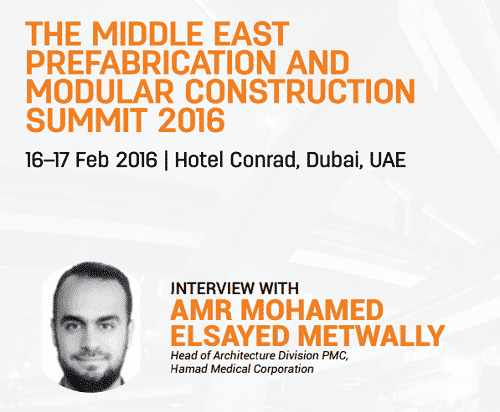
Amr