The Middle East Prefabrication and Modular Construction Summit 2016 – 16- 17 Feb 2016 | Dubai, UAE
What are the construction challenges being faced in GCC market and how precast technologies are helping in solving those challenges?
The region’s construction sector is preparing for the next boom with extensive infrastructures projects being planned. To meet the expected rising construction needs in the region, JVs and business relationships between foreign and local companies are growing to develop not only new hotels, residential, commercial buildings but also new roads and highways, rail tracks and rolling stock, power plants, deep sea ports, airports and industrial estates and other key projects which are also attracting investments and capital and expertise from Japan, Korea, Europe amongst others.
Against such a background in the GCC construction sector, cost effective sourcing and logistics of construction materials, better construction techniques and heavy equipments while securing skilled and unskilled manpower are critical challenges for regional and local contractors as well as project developers. This is where pre-cast construction technology and this summit adds critical value.
How are precast and prefab construction technologies helping in the cost effective delivery of the projects?
Pre-stressed member are crack-free under working loads and, as a result, look better and more watertight, providing better corrosion protection for the steel. Many projects find that pre-stressed concrete provides the lowest overall cost, considering production and lifetime maintenance.
The precast concrete double-wall panel with insulation (fiberglass, plastic, etc.) achieves better thermal performance. Also besides their energy efficiency and aesthetic versatility having finished or textured surfaces on both sides, they also provide excellent noise attenuation, outstanding durability (resistant to rot, mold, etc.), and rapid construction.
Precast concrete sandwich wall panels have been used on virtually every type of building in the GCC, including schools, office buildings, apartment buildings, townhouses, condominiums, hotels, motels, dormitories, and single-family homes. Although typically considered part of a building’s enclosure or “envelope,” they can be designed to additionally serve as part of the building’s structural system, eliminating the need for beams and columns on the building perimeter.
How active is public procurement on involving and encouraging private industry players in absorbing precast and prefab methods of construction?
Modular precast is a smart way to build any type of buildings safely, affordably and resource-efficiently. It ensures faster construction times, better quality and lowers total construction costs considerably while having lower lifetime costs than any other building solution. Still, requirements for beautiful, modern buildings are not compromised. Public sector has been actively pushing for more cost efficient techniques in construction.
Compared to cast-in-situ, precast uses less of everything – less cement, less water, less steel, and less labor and works in virtually all environments – cold, hot, moist or dry. It produces less waste on the site and in the factory. This makes CO2 footprint of precast much smaller than in cast-in-situ construction. Furthermore Material handling is easier and less scaffolding is needed. In addition, the forms used in a precast plant may be reused multiple times before they have to be replaced, which allow cost of formwork per unit to be lower than for site-cast production.
What are the exemplified usages of precast construction elements?
Precast suits well for any type of building or infrastructure as a whole or as components. In the Middle East region, pre-cast elements have been used as sandwich, plastered sandwich Façades for both high and medium rise buildings which can be free-standing walls used for landscaping, soundproofing, security walls, and some can be Pre-stressed concrete structural elements. Other elements include, floors slabs being hollow-core, half, ribbed or solid slabs, partition and internal, foundations piles, buildings and bridges frames with beams, multi-story car parks, modular paving, railway tracks, stairs, shafts, manholes, storm water drainage, water and sewage pipes, tunnels and other special products like silos, fencing , floating docks , retaining walls etc. Thus Precast can be made into any shape or color and finished with several techniques. This together with longer spans gives architects and other designers more freedom than ever.
How are you interacting with precast and prefab industry? How is it helping you and what are the specific challenges you are facing?
In the United States, a precast plant need to be certified to supply their products to a construction site sponsored by the state or federal Government. Certification is done thru the Architectural Precast Association (APA), National Precast Concrete Association (NPCA) with focus on utility, underground, and other non-pre-stressed products while the Precast Pre-stressed Concrete Institute (PCI) certification focus on pre-stressed concrete elements used in above ground structures such as buildings, parking structures, and bridges. This is lacking in the region.
How do you rate the topics of discussions at the summit?
Attendance of this summit with the extensive networking sessions and interactive discussion with experienced panelists will be invaluable for those involved or keen to seek opportunities or cementing partnerships in the Pre-Cast Concrete Technology & Manufacturing sector in the region to manage pivotal desired LowCost challenges in both Housing and Transportation Infrastructure (Roads, Bridges & Highways) Projects critical to the re-emerging construction sector.
Loay Ghazaleh was interviewed by the team at Information Exchange Group (IXG) ahead of their upcoming event The Middle East Prefabrication and Modular Construction Summit 2016.
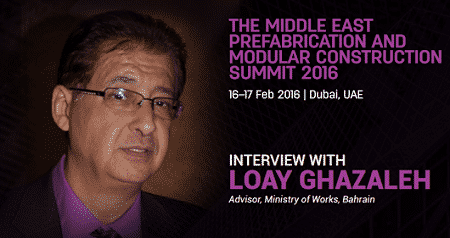
loay